Capabilities
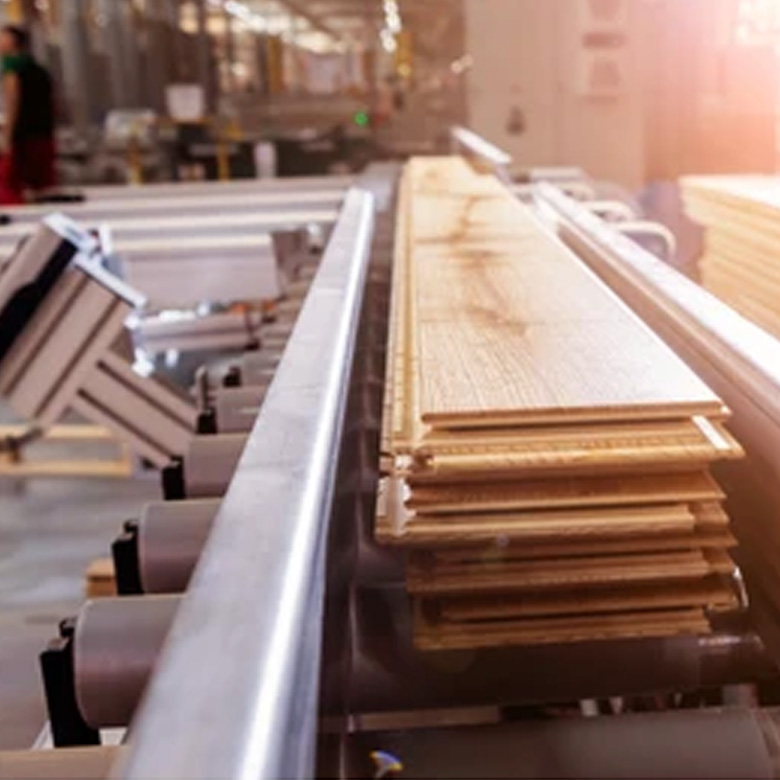
Utilizing available technology and a variety of advanced machinery operated by highly trained people we take pride in delivering precision and excellence in every project.
By implementing advanced CAD software and CNC automation, we ensure meticulous accuracy, optimize material yield, and minimize waste—reflecting our unwavering commitment to sustainability and efficiency.
Our knowledge of and in the use of a wide range of materials, including emerging and innovative options, enables us to bring even the most unique ideas to life. With the use of computer software, we conceptualize our clients’ visions and provide realistic renderings of the finished product, ensuring their expectations are met before production begins.
The combination of state-of-the-art machinery, skilled labour, and personalized solutions makes Aspen a fully customizable and expertly dedicated millwork shop, capable of turning concepts into exceptional creations.
Processes and Procedures
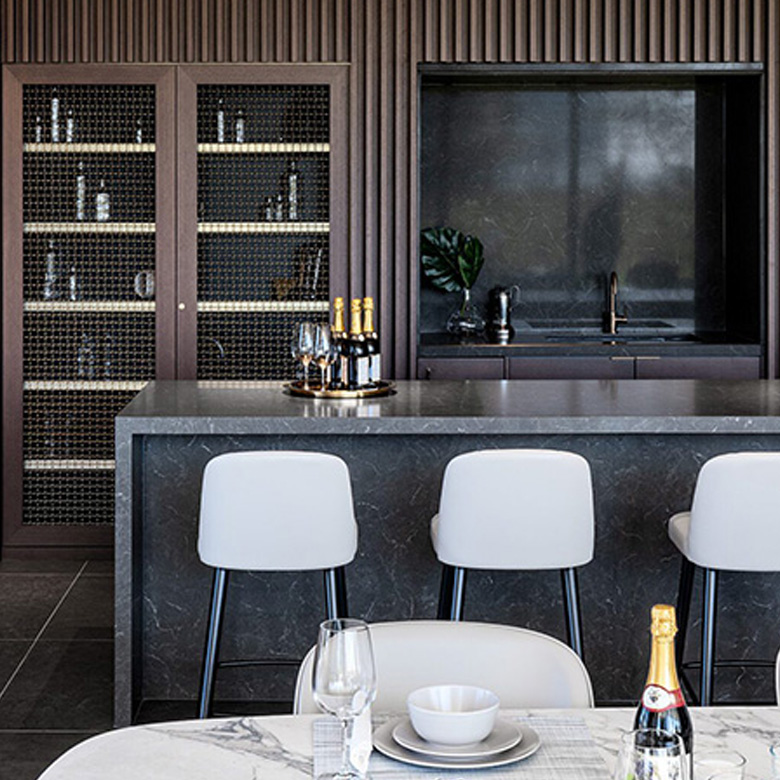
It all begins with an initial consultation.
Here we collaborate with our clients to understand their requirements and to gather information with the use of images and hand renderings prior to actual design. At this stage we also discuss budgets so that we can design our millwork accordingly. Second stage is to create preliminary computer renderings so that they can be presented to clients, discussed and altered so that a final drawing can commence. We also present and aid in selecting materials, hardware, and finish options ensuring that all elements are considered. The final stages are production and installation. This is where initial concepts have come to life, are fit into its space and are now a reality for years to come.
Technology and Innovation
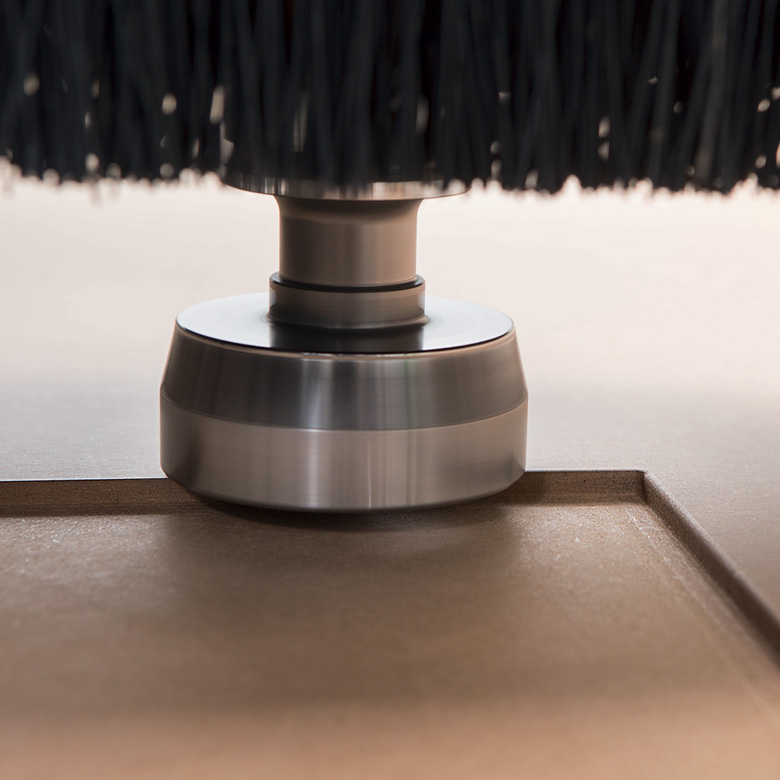
Advanced equipment and tooling enable us to deliver precision and quality.
With the utilization of CAD software for 3D modeling, CNC automation for precision joinery we are able to conceptualize client visions with realistic renderings, ensuring customer alignment prior to production. The benefits of our technology are clear: faster turnaround times, optimized material yield, and superior craftsmanship. Our techniques ensure every product is tailored to perfection while maintaining efficiency and sustainability.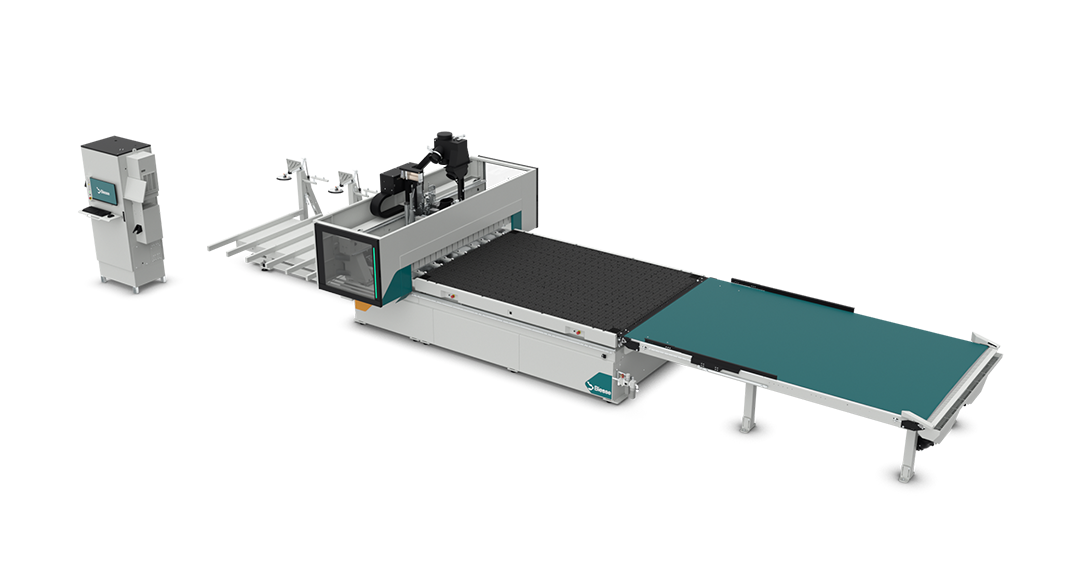
Biesse Rover K FT 1536 3 Axis CNC
CNC
A flat table nesting CNC offers major advantages for a woodworking company by streamlining production, reducing material waste, and boosting accuracy. It uses nesting software to optimize sheet layouts, cutting all parts in one automated run with high precision. This not only saves time and labor but also ensures consistent quality and cleaner cuts with less finishing required.
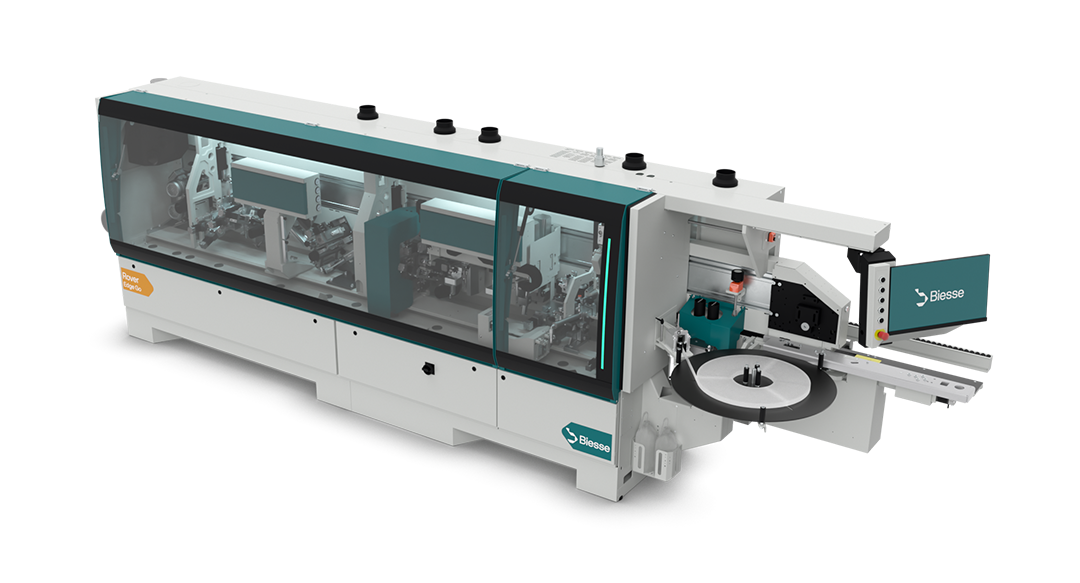
Biesse Akron 1330 Edgebander
Edgebander
An edgebander allows us to apply a clean, finished edge to raw-cut materials, creating a seamless and durable surface. This added edge not only enhances the appearance but also protects the part from moisture, chipping, and everyday wear. By automating the process, edgebanders deliver faster, more accurate, and highly consistent results—making them essential for cabinetmaking, and high-volume woodworking operations.

Cross Air Technology Spray Booth
equipped with
Graco Pro Mix II 24ft Deep x 13ft wide
Spray booth
Having an in-house spray booth with the Graco ProMix II allows us to take full control of the finishing process. The ProMix II ensures accurate mixing of two-component materials, leading to consistent, high-quality finishes. With an in-house booth, we reduce turnaround times, minimize material waste, and have the ability to address quality issues immediately. It also increases flexibility, enhances control over production, and helps maintain a smooth, efficient workflow.